Transforming Industrial Laundries
With Robotics and Automation
Let our robots do your heavy work
Our solutions
We revolutionize industrial laundries worldwide
With the aim of increasing efficiency and minimizing the tedious work in laundries worldwide, we have developed solutions for efficient mat rolling, automatic soiled side sorting, and smart stack management for more than ten years.
Known for innovative automation solutions combining artificial intelligence and simple mechanics, we have started a revolution in the industrial laundry industry.
Let robots do your heavy work
and create a better and safer work environment
Let us sort it out
Automating the most manual processes
As a Danish robotics company, we develop advanced software and smart machinery to automate workflows in the industrial laundry industry.
Located in the city of Odense, we profit from the strong network with
industry-leading robotics companies as well as renowned educational institutes for software and robotics such as the University of Southern Denmark.
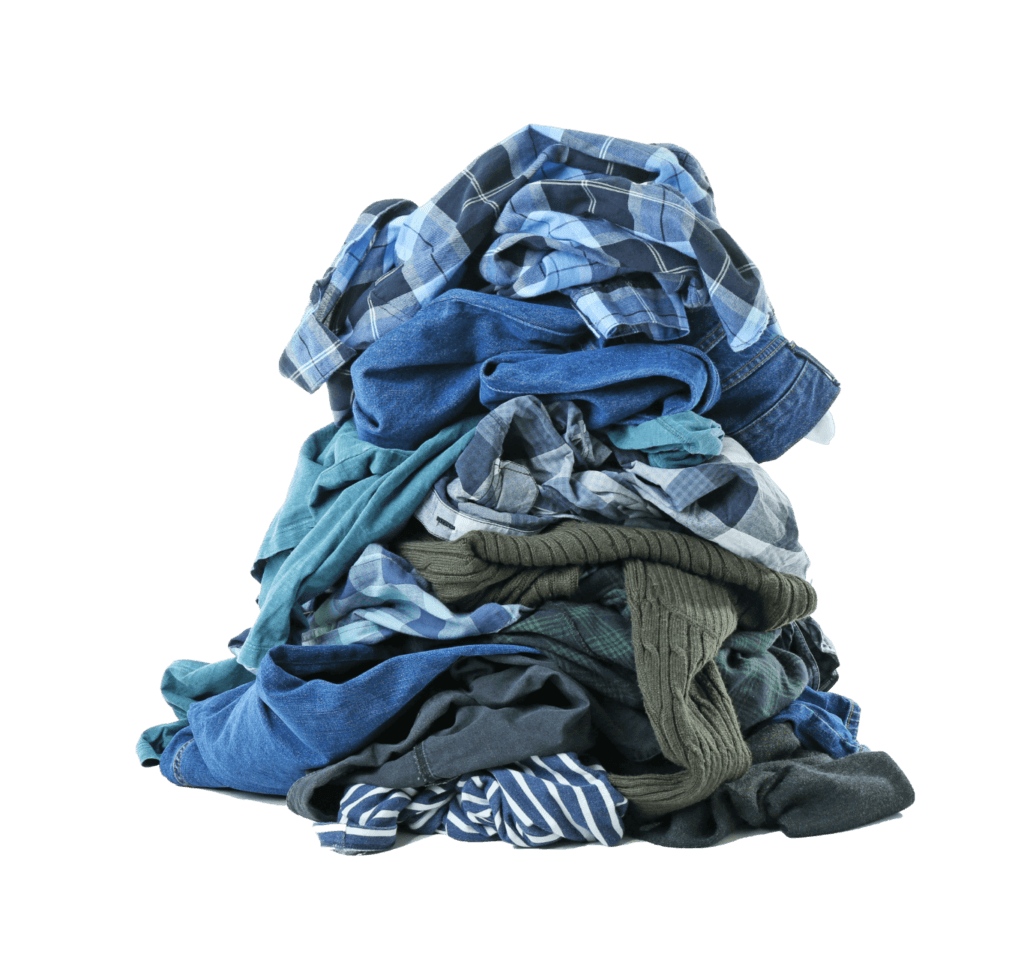
Meet our customers
Success stories around the world
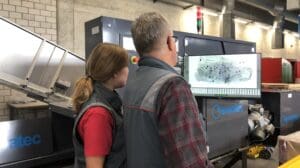
X-ray scanner ODIN supports detecting foreign objects for the Swiss Army
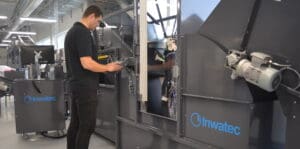
Berendsen merges United Nations Global Goals into strategy
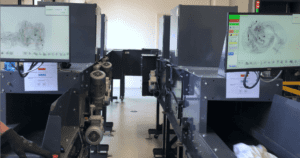
Alsco Padova’s customers ask for traceability – RFID sorting provides it
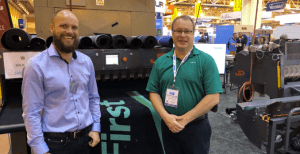
VORTEX mat rollers help Unifirst improving productivity
The dream team
Passionate and dedicated


The Inwatec Benefit
Modular and flexible: designed for your needs
Modular Components
Our modules are fully customizable for ultimate felxibility – tailored to your specific needs.
Easy Maintenance
Local support from the JENSEN-GROUP and remote assistance from Inwatec ensure quick problem solving – anywhere, anytime.
Simple Engineering & Easy Operation
Simple design, smart software. No need for specialized engineers – your existing team can handle our machines.
Employee Satisfaction
Automating tedious tasks frees up your team for more complex responsibilities and makes for a safer work environment.